Method Statement For Installation Of Air Handling Unit
Below is the method of statement for the installation and testing of AHU & FAHU i.e. Air handling units. We have given only three steps which are necessary tools. Method Statement Installation & Commissioning Method Statements. Be the first to review “Testing & Commissioning of Air Handling Units” Click here to cancel reply.
- Method Statement Electrical Installation
- Method Statement For Installation Of Sheet Pile
- Method Statement For Installation Of Lv Cables
Advertisement. Fork Lift or Crane with capacity & arrangement in line with the Manufacturer’s recommendations, pallet mover and as required at site.
Hydraulic Trolley. Portable hand tools. Portable Drilling Machine/ Grinding Machine & Angle Cutter. Spirit Level / Level Threads.
Scaffolding with platform. Material Handling & Storage On receipt of the Air Handling Units and accessories at site, necessary precautions shall be taken for unloading, shifting & storage, as follows:-. All Air Handling Unit received at site shall be inspected and ensured that the materials are as per approved material submittals in terms of their make, model type, point of origin and capacity. Upon arrival at site, the Air Handling Unit shall be off-loaded carefully at site by the Site Engineer / Site Supervisor using necessary manpower and required equipment to ensure that no damage is caused to the Air Handling Units. At site all the Air Handling Units will be stored in a clean / dry place and adequate covering by tarpaulin sheets will be done to protect the equipment from deposition of construction dust till it is finally shifted to its location.
Any discrepancies, damage etc., found will be notified and reported for further action suitably. GENERAL INSTALLATION REQUIREMENTS. Ensure that the proper clearance is available from civil side before commencement of works. Ensure that the work area is clean and safe for carrying out the activities.
Prior to start of works, it shall be ensured that the relevant shop drawings and coordination drawings are approved and issued for construction. It shall be ensured that no contradiction with other previously installed services, and if there is any shall be cleared. It shall be ensured that the material issued is as per the approved material submittal. INSTALLATION PROCEDURE FOR AIR HANDLING UNIT AHU’s.
The following procedure shall be followed for the installation of Air Handling Units. Visually inspect the exterior casing of the Air Handling Units for any damages during transporting and transferring of the units. Materials shall be submitted for Consultant approval before proceeding with installation.
Cut all banding (if applicable) loose from skid but do not remove the skids until the unit is shifted to the installation area. Site Engineer shall ensure that the installation of the Air Handling Unit is carried out in accordance with manufacturer’s installation recommendations and specification. Prior to start of installation, refer to the approved shop drawing related to the area of installation and ensure that required material is available at site as per approved material submittals. Ensure that the equipment and accessories are stored properly and there is no damage or deformity of any kind during transportation of material from site store to the working area. After inspecting the work area, ensure that it is totally ready for installation.
Then the required equipment shall be moved to the place of installation. Check the equipment weight to ensure that the rigging equipment can handle that safely. Before installing the unit check whether proper space is available for unit servicing, installing and removing air filters or not. Proper marking shall be done for the unit location / supports as per approved shop drawing. Ensure the unit model number location shall be same as indicated on the drawing. Ensure that the orientation of AHU’s is matching with direction of supply and return duct. After inspecting the work area / foundation, ensure that it is totally ready for installation. Then the required equipment shall be moved to the place of installation. Under direct supervision of the Site Engineer / Site Supervisor, lift the air handling unit, transfer it to the allocated places as per approved shop drawing, position it on to the plinth using the crane if required or rolling as appropriate and feasible.
Assembling of the air handling unit shall be done by aligning the sections by using the matching bolt of each sections and proper gaskets supplied by manufacturer, then tighten the bolts and make sure that the complete unit is resting properly on the rubber pads / spring isolators. Use proper gaskets as supplied by manufacturer while assembling the modules. Manually rotate the fan wheel to ensure free movement of the shaft and bearings. Check the base is free from corrosion and galvanized coating is applied, If required.
Inspect the coils for fins damage. Check all the filters are fixed properly. Duct work shall be connected to AHU’s with Flexible Duct connector as per approved material submittal for supply, return and fresh air duct connections. Duct thermostat ( sensor ) and test point shall be installed as per approved shop drawing.
Connect the piping net work to the air handling unit as per the approved drawing. Pipe work shall be connected to AHU’s with flexible connection. And ensure that all valves and control devices has been installed.
Condensate drain pans shall be connected with pipe by using approved material submittal. Condensate drain pipes shall be directly connected to the traps and all condensate drain pipe shall be insulated as per approved method statement. Appropriate trap shall be provided as per approved drawings. Flushing & cleaning of system shall be done as per method statement which shall be submitted separately.

Equipment, pipe identification, tagging & labeling shall be carried out after completion of all works as per approved material submittal / Specification. The V belt shall be checked for proper tension. All control devices, frequency drives application shall be as per approved BMS submittal.
Below is the method of statement for the installation and testing of AHU & FAHU i.e. Air handling units. We have given only three steps which are necessary tools, installation and testing procedure. Other parts should be included for preparation of professional method statements for approval purposes etc.
Other sections may include Purpose, Scope, Responsibilities, Standards, references and attachments etc. Required Tools For AHU Installation. Grinding/Cutting Machine. Mechanical Toolkit.
Drill machine. Crane / Chain Block. Supports, anti-vibration rubber pads. Nuts, bolt, gaskets, bolts. Valves Preparation & AHU Pre Installation Requirements. Check the AHUs/FAHUs foundation and ensure it is as per approved drawings.
Check the area around the foundation and ensure access to the AHUs/FAHUs from all sides as applicable. Ensure availability of sufficient slope to the drainpipe, for easy draining of condensate drain. Place the anti-vibration ribbed rubber pads of correct thickness as per approved drawings/submittals. In case of multiple rubber pads the pads shall be placed one above the other, with the ribs at right angle to each other. AHUs/FAHUs sections are assembled at site/location by factory trained personal if required by consultant. Installation of Air Handling Units AHU & FAHU. Advertisement:.
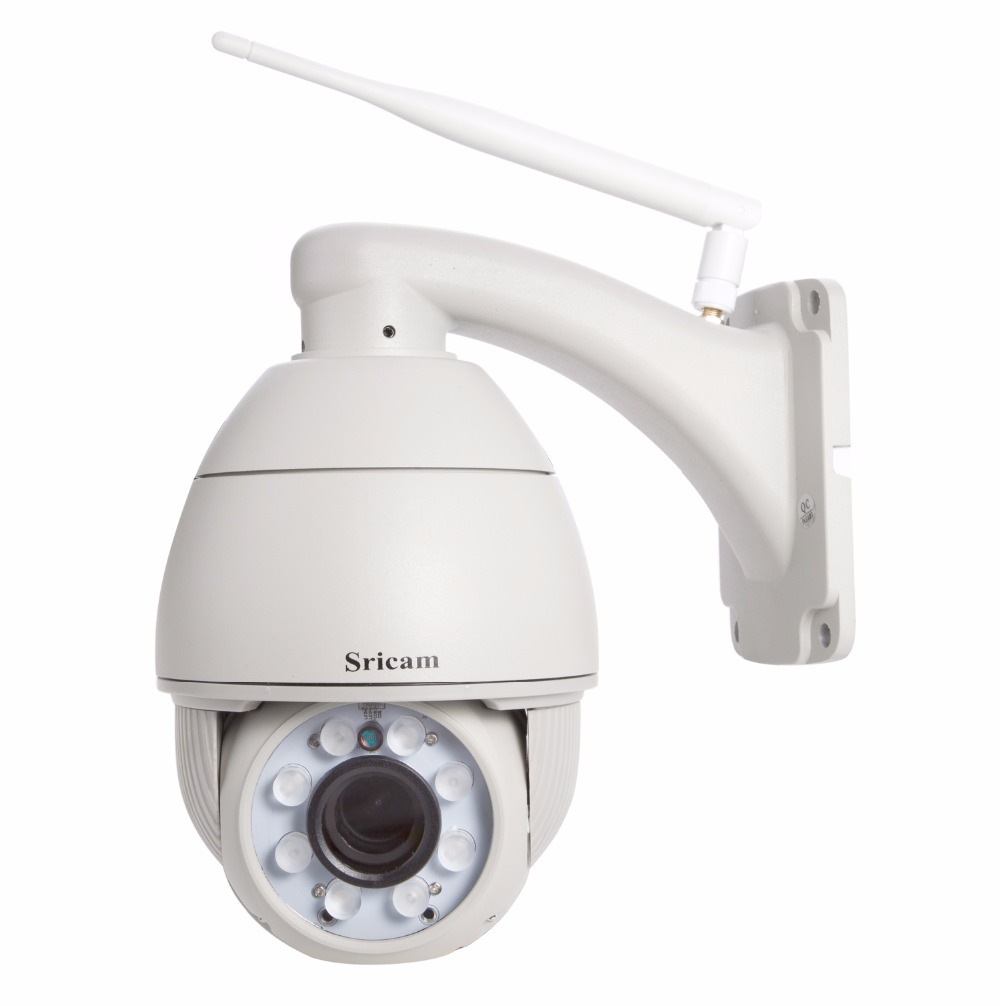
Shift the AHUs/FAHUs to the place of installation in safe manner using fork lift and crane as applicable. Ensure that the correct AHU is shifted to the place of installation. Air inlet, outlet, fresh air connection and chilled water connection orientation are as per approved drawings. If the AHUs are shipped in multiple sections, the AHUs will be assembled strictly as per the manufacturer’s instructions, and also consider:The AHUs/FAHUs are placed correctly on foundation with vibration isolator rubber pads at right location.Identify the correct sections that are to be bolted together. Position fan section on housekeeping pad. Install gaskets at all bolted joints that are required to be joined. Position the next section, to be joined, carefully on housekeeping pad, align the two sections.
Jointing brackets will then be used to externally join the sections together. AHUs/FAHUs shall be inspected again for any damage during hoisting/shifting. Upon satisfactory positioning of AHUs/FAHUs any open air/water outlets of AHUs/FAHUs shall be closed properly and area shall be cleaned, complete protection in areas where other trades are working. Air, Chilled water, Electrical and Condensate Drain connections. Ducting connection shall be done as per approved shop drawings. Provide flexible duct connections as applicable/as approved submittal.
Method Statement Electrical Installation
Provide proper supports as per approved drawings. Chilled water connections shall be made as per approved drawings.
Method Statement For Installation Of Sheet Pile
Ensure supply and return connection is made properly. Provide pipe flexible connection and other piping accessories as per approved drawings and submittals. The piping shall be free of any strain and shall not exert any load on AHUs/FAHUs. Install the control valves, strainer, commissioning set correctly as per direction of flow as per approved drawings and project technical specification.
Ensure proper operation of valve handles and sufficient space for valve installation. Electrical power connections shall be done as per approved drawings. Condensate drain piping shall be terminated at the nearest floor drain. Provide the `U’ trap in the condensate drain piping and provision for cleaning of `U’ traps, also ensure proper slope to enable easy drainage of condensate water. The piping connections to AHUs/FAHUs shall be pressure tested to 1.5 times the working pressures. Coils not included in test. Strainer shall be cleaned after pressure testing and initial flushing of chilled water piping system.
Flow test of the AHUs drain tray should be done for condensate drain pipe and ensure water is drained out completely. Inspection and Testing Of AHU Installation All construction/inspection/testing works shall be carried out in accordance with specifications. Work shall be carried out by the site MEP staff under the guidance of respected Engineer and shall further be checked and approved by quality engineer. An inspection request for the AHUs/FAHUs installation shall be submitted at least 1-2 days prior to the client/consultant or as agreed. Heat recovery testing will be done to ensure smooth operation. Check the unit model number and relevant accessories are available.
Method Statement For Installation Of Lv Cables
Unit name plate as per order. Verify the construction of the house keeping base is as per the specification & drawing for floor mounted AHU. Verify the presence of approved vibration isolators, installed before the installation of AHU. Check anti-vibration mountings are located correctly. Service space around the unit as per manufacturer requirement. Check the duct is connected to AHU with proper flexible connections.
Check fan moves freely. Check the level of the AHU and verify the minimum slope as per drawing in the direction of condensate pipe. Check the drain connection with U trap.
Check filters are provided as per specification. Verify the electrical connection of AHU with control panel as per construction drawing. Check and verify all Installation as per approved drawings. After installation inspect the AHU for physical internal and external damages. Verify the absence of any vibration in AHU and its inner like fan, motor and coils etc. Verify the process pipe connection with AHU along with valves, accessories and flow switch etc.
Confirm the additional adequate support for all fittings and valves near AHU as per construction drawings. Verify the installation of 2-way modulating & gate valve of approved brand and quality as per approved material. Verify the presence of identification labels, safety and warning signs at their positions as per approved materials.